What rules do PCB designs need to follow?
- eguidezhan
- Sep 7, 2023
- 8 min read
Whether you're engaged in high-speed activities or designing high-speed printed circuit boards (PCBs), adhering to sound board design practices is essential to ensure your designs function as intended and are poised for mass production. In this guide, we've consolidated fundamental PCB board design and layout principles applicable to most contemporary boards. While professional designs may necessitate additional layout guidelines, the following PCB layout guidelines serve as a strong foundation for most board designs.
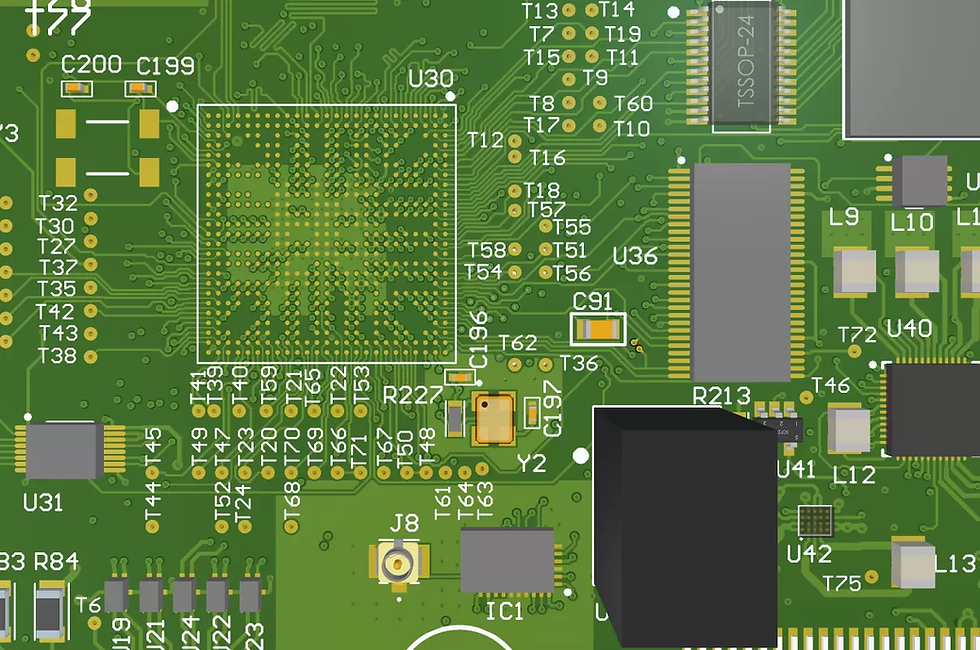
Establish PCB Board Design Rules Before Commencing Layout
When embarking on a new PCB design, it's easy to overlook the crucial design rules governing the project. Identifying key clearances early in the design process can mitigate the need for extensive component repositioning and rerouting later on. So, where can you access this vital information?
The initial approach is to engage with your chosen PCB fabrication partner. Reputable manufacturers typically publish their capabilities online or provide comprehensive documentation. If this information isn't readily accessible on their website, consider reaching out via email to inquire about their capabilities. Ideally, this should be done prior to commencing component placement. When you do contact them, ensure that you submit your proposed overlay for their review, or consult their standard overlay data.
Once you've obtained their list of capabilities, perform a comparative analysis against the industry reliability standards you plan to adhere to (e.g., Class 2 vs. 3 or professional standards). Upon identifying these critical parameters, opt for the more conservative design layout constraints required to ensure both manufacturability and reliability. Subsequently, encode these constraints into your PCB board design rules.
As you progress through the layout phase, your board design rules will serve as a safeguard against most design errors that can lead to manufacturing and assembly complications. After configuring the board design rules, you can initiate the layout process.
These fundamental PCB board design practices will fortify your designs, enhancing their manufacturability and reliability. While each project may entail specific requirements, adhering to these core guidelines will invariably result in more robust and dependable PCBs.
Optimizing Component Placement for Efficient PCB Layout Design
Fine-tuning component placement during the PCB layout design process is both an art and a science, demanding meticulous consideration of the valuable real estate available on the board. The primary objective of component placement is to create a board that facilitates easy routing, ideally with minimal layer transitions. Moreover, it must adhere to design rules and fulfill the required component placement criteria. Striking a balance among these aspects can be challenging, but a structured approach can assist board designers in placing components that satisfy these demands:
Prioritize Prerequisites: Frequently, certain components must be situated in specific locations, often due to mechanical enclosure constraints or their physical dimensions. It is prudent to begin by placing these components first, securing their positions before proceeding with the remainder of the layout.
Strategically Place Major Processors and ICs: Components such as high-pin-count ICs or processors frequently necessitate interfacing with multiple elements in a design. Centralizing these components simplifies trace routing in the PCB layout.
Minimize Net Crossings: Unrouted nets are typically apparent when components are positioned on the PCB layout. It is advisable to minimize the instances of net crossings, as each network intersection entails a layer transition through vias. Creative component placement that eliminates net crossings can significantly ease the implementation of optimal routing guidelines for PCB layout.
Adhere to SMD PCB Board Design Rules: It is prudent to position all surface-mount device (SMD) components on the same side of the board. This recommendation stems from assembly considerations; each side of the board necessitates its own SMD soldering process, and consolidating all SMDs on one side can mitigate additional assembly expenses.
Experiment with Component Orientations: Components can be rotated to mitigate network intersections. Exploring orientations where connection pads face each other can simplify routing challenges.
Careful Planning of Power, Ground, and Signal Traces in PCB Layout
Now that components are strategically placed, the next crucial step in the PCB layout design process is routing power, ground, and signal traces to ensure clean and error-free signal transmission. Here are some key considerations to bear in mind during this phase:
Power and Ground Plane Placement
Typically, power and ground planes are allocated to the two inner layers of the PCB. However, with a 2-layer board, this arrangement may not be as straightforward. In such cases, you'll need to designate one layer for a substantial ground plane and route signal and power traces on the other. For PCB stack-ups with four or more layers, employing a dedicated ground plane is preferable over attempting to route ground traces. In instances where components require a direct connection to the power supply, it's advisable to employ a common rail per power supply, ensuring that you incorporate adequately wide traces (around 100 mils for 5 to 10 Amps) and avoid daisy-chaining power lines from one component to another.
While some recommendations suggest symmetrical layer placement for ground planes, it is not always mandatory for fabrication. In the case of large boards, symmetrical layer placement may be necessary to reduce the risk of warping. However, on smaller boards, this concern is typically negligible. The primary focus should remain on providing efficient access to power and ground and ensuring that all traces establish strong return path coupling to the nearest ground plane. Achieving perfect symmetry in the PCB design stackup should be secondary to these priorities.
Routing Guidelines in PCB Layout
Subsequently, establish connections for signal traces to align with the nets in the schematic. Best practices in PCB layout emphasize the placement of short, direct traces between components whenever feasible, although this may not always be achievable in larger board designs. If the component placement dictates horizontal trace routing on one side of the board, ensure that the other side predominantly features vertical traces. This is a fundamental guideline, especially in the realm of 2-layer PCB design.
As the number of stacked layers increases, the complexities of adhering to PCB layout rules and guidelines intensify. Your routing strategy will necessitate alternating horizontal and vertical traces on different layers unless reference planes are employed to segregate each signal layer. In intricate boards designed for specialized applications, some widely accepted PCB best practices may no longer apply, making it imperative to adhere to PCB board design guidelines tailored to the specific application's requirements.
Defining Trace Width
Traces serve as the connective pathways between components in PCB layout design. However, determining the appropriate trace width depends on three critical factors:
Manufacturability: Traces must not be so thin that they become prone to unreliable manufacturing. In most cases, trace widths significantly exceed the minimum manufacturable width provided by manufacturers.
Current: The magnitude of current flowing through the trace influences the minimum width required to prevent the trace from overheating. Higher currents necessitate wider traces.
Impedance: High-speed digital or RF signals demand specific trace widths to achieve the desired impedance value. This is not applicable to all signals or nets, and impedance control is only essential for specific signals in your PCB design.
For traces that do not require precise impedance control or carry high currents, a trace width of 10 mils is generally sufficient for most low-current analog and digital signals. Traces handling more than 0.3 A may need to be wider. To determine the suitable trace width, you can employ the IPC-2152 nomogram, which considers current capacity and temperature rise limitations in PCB design.
Thermal Connections for Through-Hole Components
Ground planes in PCB design act as expansive heat sinks, ensuring even heat distribution throughout the board. Consequently, if a particular via connects to the ground plane, omitting the thermal pad on that via will facilitate the conduction of heat to the ground plane, preventing it from being trapped near the surface. However, this approach can present challenges when employing wave soldering for through-hole component assembly, as it is essential to retain heat near the surface during this process.
Thermal dissipation constitutes a critical PCB layout design feature, particularly when fabricating boards through wave soldering or assembling through-hole components that directly connect to planes. Achieving optimal process temperatures is challenging when vias serve as solder joints directly linked to the plane. In such scenarios, using a heat sink can help maintain soldering temperatures. The core principle of heat dissipation is straightforward: it decelerates heat dissipation into the plane during soldering, mitigating the risk of cold solder joints.
While some designers advocate using thermal patterns for any via or hole connecting to internal ground or power planes, this advice may not apply universally. The necessity for thermal vias on through-hole components depends on the copper plane or polygon sizes that form the connection on inner layers. Careful consideration and consultation with manufacturers are essential to determine the appropriate thermal dissipation strategy for your specific PCB design.
Effective Component and Thermal Management in PCB Layout Design
In PCB layout design, adherence to well-defined routing guidelines is crucial to both streamline the routing process and prevent electrical interference. These guidelines also play a pivotal role in efficient thermal management, especially when dealing with high-power components that tend to generate heat. Here, we delve into the strategies for component grouping and separation, essential for ensuring an organized and interference-free PCB layout.
Component Grouping
Efficient PCB design often involves grouping specific components together within the layout. This grouping stems from the recognition that some components are intrinsically linked within a circuit and must only connect to each other. As such, there's no necessity to scatter these components across different regions or sides of the board. Instead, PCB layout design becomes an exercise in organizing and arranging clusters of circuits to facilitate seamless tracing.
In many layouts, you'll encounter a mix of analog and digital components, and it's imperative to prevent digital components from interfering with their analog counterparts. A decades-old practice involved segregating ground and power planes into distinct sections, but this approach is no longer considered viable in contemporary board designs. Unfortunately, some outdated board layout guidelines still advocate this practice, leading to suboptimal layout practices that can induce electromagnetic interference (EMI).
The recommended approach is to utilize a continuous ground plane beneath the components, avoiding the physical division of the ground plane into sections. It's essential to group analog components that operate at similar frequencies together and likewise for digital components. Visualize each component type occupying a designated area above the ground plane within the PCB layout, all while maintaining a unified ground plane throughout most board designs.
Separation of High-Power Components
In certain scenarios, it is prudent to isolate components on the board that dissipate substantial heat into distinct areas. This separation serves the purpose of evenly distributing temperature across the PCB layout rather than concentrating heat-emitting components into specific hotspots, which could be detrimental.
To achieve this, begin by identifying the "thermal resistance" rating specified in the component's datasheet. Utilize this information to calculate the anticipated temperature rise based on the estimated heat dissipation. In some cases, incorporating heat sinks and cooling fans may be necessary to mitigate component temperatures.
During the development of your routing strategy, you'll need to strike a careful balance between the placement of these high-power components and the goal of maintaining short trace lengths, a challenging task that requires meticulous consideration.
By following these component grouping and separation strategies, PCB layout designers can create well-organized and thermally efficient layouts while minimizing the risk of electrical interference, ultimately contributing to the overall performance and reliability of the printed circuit board.
Ensuring PCB Design Excellence and Accuracy
As you near the culmination of a PCB design project, it's common to encounter a surge of activity as you piece together the final elements for manufacturing. This critical phase demands meticulous scrutiny, as errors at this juncture can potentially determine the project's success or failure.
To bolster this crucial quality control process, commencing with an Electrical Rule Check (ERC) and a Design Rule Check (DRC) is strongly advised to ensure adherence to established constraints. With both systems at your disposal, you can readily define parameters such as gap widths, trace widths, pertinent manufacturing prerequisites, high-speed electrical criteria, and other physical specifications tailored to your specific application. This mechanizes the validation of PCB design layout review guidelines, affirming the integrity of your layout.
It's worth noting that various design workflows stipulate that a design rule check should be performed at the conclusion of the board design phase, as preparations for manufacturing ensue. Nevertheless, by utilizing the appropriate design software, you can execute checks throughout the design journey, enabling early detection and swift correction of potential design issues. Upon obtaining error-free outcomes from the final ERC and DRC assessments, it's advisable to conduct a thorough signal routing examination, meticulously scrutinizing each signal's path to ensure comprehensive coverage, and corroborating this by tracing the schematic one wire at a time.
Concluding TechSparks' top PCB layout tutorial for most board designs, while the list of recommendations may seem succinct, it serves as a robust foundation for designing a fully functional, manufacturable board within a condensed timeframe. These PCB board design guidelines represent just the tip of the iceberg, yet they furnish the bedrock for an ongoing enhancement practice that permeates and sustains all design endeavors.
Commenti